We don’t have to tell, but there is a constant struggle between being proactive and reactive in the facility management industry. Taking a reactive approach may seem easier in the short term. However, it often leads to a myriad of challenges and drawbacks that can have detrimental effects on the overall efficiency and performance of the facility. Implementing a reactive approach results in increased costs due to expensive repairs and replacements.
There is little doubt you made the right decision in choosing a proactive approach to managing your facility. In this article, we share popular strategies for adopting proactive maintenance into facility management. Once you implement these strategies, you will be in a better position to reap the benefits of reduced costs and more informed decision-making.
What is proactive maintenance?
According to the Aberdeen Group study, organizations that implement proactive maintenance can save an average of 10% on maintenance costs, reduce unplanned downtime by an average of 25%, and increase equipment lifespan by an average of 20%.
Proactive maintenance is a strategic approach to facility management that focuses on anticipating and preventing issues before they occur. Unlike reactive maintenance, which involves addressing problems as they arise, or preventive maintenance, which involves scheduled maintenance tasks, proactive maintenance aims to stay one step ahead by actively monitoring equipment and taking preventive measures.
By adopting a proactive maintenance strategy, facility managers can
- Increase asset availability
- Identify potential equipment failures early on
- Prevent unplanned downtime
- Reduce maintenance costs
FSM Software: A Must Have For Facility Managers. Start Your Free Trial.
Maintenance strategies for proactive facility management
1. Implement automated analytics to predict downtime
Automated analytics can help you identify potential maintenance issues before they become costly repairs. This can be done by collecting data from embedded sensors throughout your property and using this data to create predictive models. These models can then be used to identify patterns and trends that may indicate the need for maintenance.
For example, you could use automated analytics to track the temperature, and humidity levels in your HVAC system. If the data shows that these levels are outside of the normal range, that could indicate that there is a problem with the system. Having advanced warning of potential issues, allows you to take corrective action before the problem causes a major breakdown.
2. Inspect and repair critical assets first
It is critical to begin proactive maintenance starting with your most critical assets first. These are the assets that have the greatest impact on your facility’s overall performance and productivity. For example, issues with the plumbing system should be prioritized over elevator failures because people can still use the stairs to get from floor to floor, but no water significantly impacts daily life.
By addressing the maintenance needs of these assets first, you can prevent expensive breakdowns and reduce the associated repair costs. While identifying your critical assets, it is crucial to involve stakeholders who have a deep understanding of the facility and its operations. Additionally, conducting a critical analysis can help determine the level of impact an asset failure would have on your business.
3. Upgrade old equipment and improve the performance of assets
Another strategic approach to facility management is focusing on upgrading old pieces of equipment. No equipment or assets will fail in a single day. If you make the extra effort to spend more time on the old equipment, you can increase the longevity and the performance of the old assets.
For example, roofing has a lifetime of about 25 years, so it is often overlooked in maintenance unless there are leakage problems. The same goes for electrical systems as well. However, once an issue arises, it can’t be easily fixed—focusing on maintaining old equipment proactively matters.
4. Use augmented reality to bridge the skill gap
Proactive facility management focuses on preventing equipment from breaking in the first place. To do this well, it is critical that you have well-trained technicians. Ineffective training will result in employees being unable to repair equipment properly. Your goal is not simply to provide training, but also to make sure the training given will better equip employees to resolve any issues they come across.
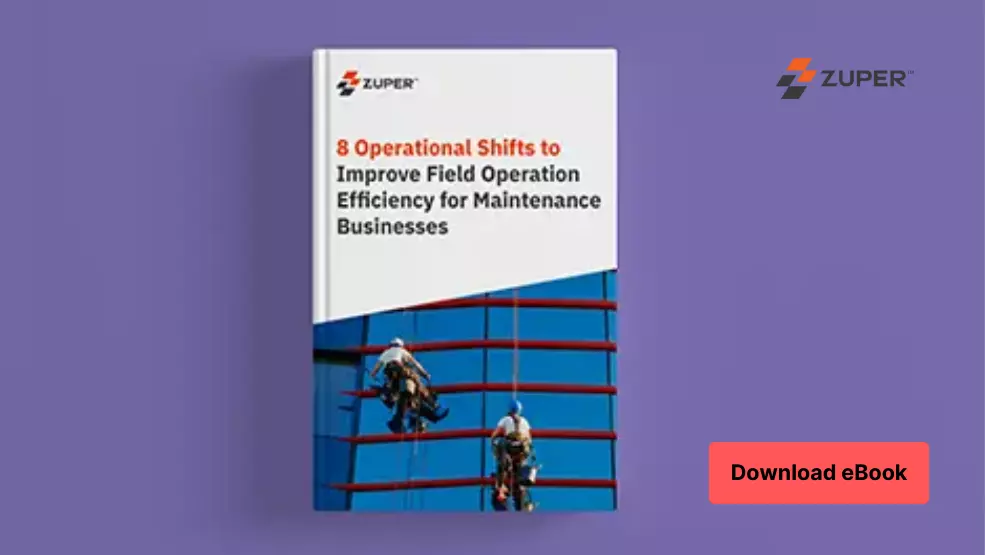
Here’s where Augmented Reality (AR) comes in. It is a tool that can be used to train your maintenance staff effectively. We can create AR simulations that let employees practice fixing different kinds of equipment. This feels like a real-time experience, and it helps you see where your staff might need more training. If they’re lacking skills in certain areas, you can give them extra training and support. This way, your maintenance staff will become more skilled and capable.
5. Use AI to reduce labor costs
For managers in charge of proactive facility management, there’s a problem—they need to spend money upfront even before anything goes wrong. Getting permission from higher-ups for this can be hard. But what if there is a way to spend less on proactive maintenance? This is where Artificial Intelligence (AI) comes in.
With AI, you can do lots of maintenance tasks automatically. This means your maintenance team can focus on more complicated and important things. For example, AI can help decide when to do preventive maintenance, keep an eye on maintenance requests, and make reports about how things are going. All of this can make your maintenance work better and smoother.
6. Implement service management and organize tasks
The next strategy in proactive facility maintenance is service management. Having a service management in place helps you organize maintenance tasks, ensuring they are planned, scheduled, and executed efficiently. By implementing service management, you will always be ready for maintenance needs. Jot down a long-term plan and set service-level agreements for all facility tasks.
For instance, think about a big office building. With service management, you can set up plans for fixing things like air conditioning, lights, and elevators. You make agreements on how fast these issues should be dealt with, depending on how important they are. Then, when something needs fixing, you know exactly when and how to do it. This kind of organization helps you see the whole situation clearly and motivates you to keep making things even better over time.
7. Streamline work orders with FSM software
Work orders are a critical tool for managing facility maintenance. From ensuring work gets done to facilitating communication between internal and external teams, work orders ensure the proper functioning of maintenance. You should streamline such important processes with field service management software.
Field service management software helps in automating your work orders, giving real-time visibility into your work orders, improving accuracy, enhancing communication, and generating in-depth reports and analytics. Check out Zuper Field Service Management Software, which stands for Automation, Digitization, and Customization.

Costs of proactive maintenance
According to a study by the Aberdeen Group, the average annual cost of proactive maintenance is $1.5 million for organizations with $1 billion in annual revenue. We cannot give away a specific amount as the costs of proactive facility management as it depend on the size and complexity of the facility. However, we can categorize the factors that factor into the costs, and they are,
- Labor for maintenance staffs
- Material costs (parts, supplies, tools)
- Travel and transportation
- Equipment downtime
How to save costs using proactive maintenance?
Proactive management is already a cost-saving approach in facility management. Rather than taking measures after the problem has come, it prevents it from happening in the first place. However, this can be a little hard for the facility managers because they have to show for expenses without any failures. However, spending some money in advance definitely pays off in the end.
Now, the question is how you can reduce money while still doing proactive maintenance. The answer is using facility management software is that you can complete the work effectively and efficiently by saving time and money spent on the workforce.
Take Zuper, for example – a facility management software that automates, digitizes, and customizes your experience. From efficient scheduling to asset and inventory management, Zuper offers a range of features that consolidate tasks onto one platform, significantly reducing proactive maintenance costs. Explore our website to discover more about how our facility management software can benefit you.
Road Ahead
Facility managers play a big role in keeping equipment working and assets in good condition. Proactive maintenance is the secret to doing this well—this means addressing small problems before they become big problems. Adopting proactive maintenance strategies is the smart way to make sure things run smoothly. By bringing these strategies into your daily routine, you can enjoy the benefits of hassle-free maintenance for years to come.
Book a free demo now and keep your assets running smoothly.
Step up and be a force for good. For every T-shirt you wear, 2700 L of water is consumed. You hold the power to reclaim gallons of water with every garment you wear. Choose minimalism; Save water. Mindful closet for a sustainable future!